今現在を「第四創業期」と位置づけ、
新たな領域に踏み出したコジマ。
めざす未来について、
キーパーソンに聞きました。
「やってみよう精神」で未来を拓く。
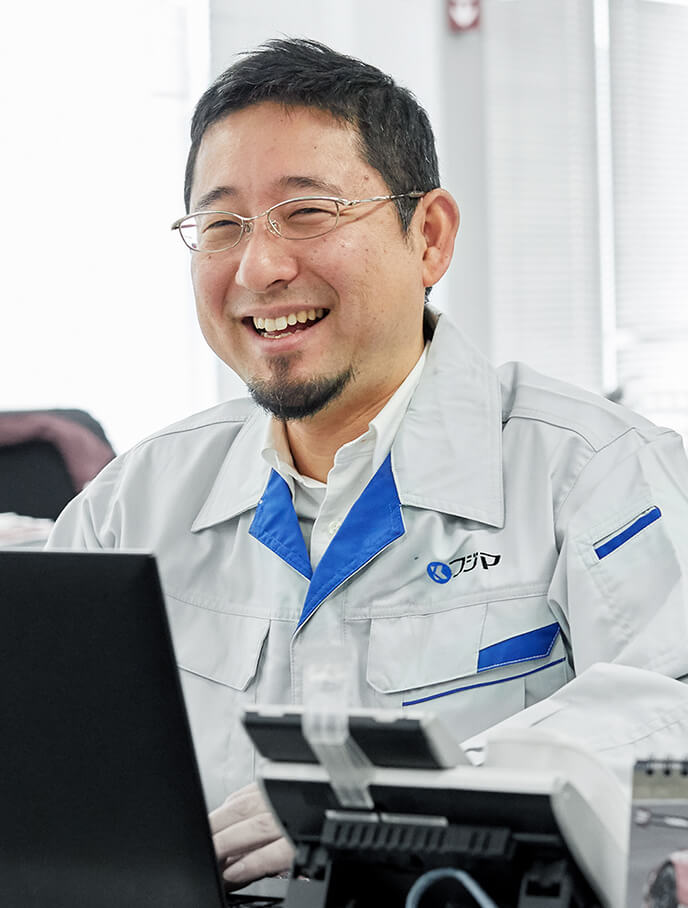
部品作りから組付、精度保証から機能保証へと領域を広げてきたコジマですが、今後はお客様と一緒にイチから製品作りを行いたい、ゆくゆくは製品企画からご提案できるようになりたいと考えています。
今すでに、お客様の設計部署にコジマの社員が出向し開発段階から並走させていただく事例が増えつつあります。ここまでこられたのはコジマに「とにかくやってみよう精神」があったから。金属部品の樹脂化に挑んだときも、インドネシアに進出したときも、前例などなかった。それでも「やってみろ」と経営陣が背中を押してくれて、チャレンジすることができたのです。おかげでお客様からは「難しい課題にもコジマなら一緒に挑戦してくれる、期待を超えてくれる」との評価をいただいています。
この先クルマはどんな進化を遂げるかわかりません。営業としては、お客様の設計部署からご信頼をいただき、未来のニーズをいかに素早く察知するかが勝負です。幸い今も、ABSセンサーやMOCといった、自動運転など次世代技術の核になる製品を手がけさせていいただいています。これからも「やってみよう」のコジマイズムで、未知の領域に貪欲にトライしていきたいですね。
部品・樹脂事業部 営業部 営業1課 課長中野 大一郎
どこに進むかわからないのが、コジマの面白さ。
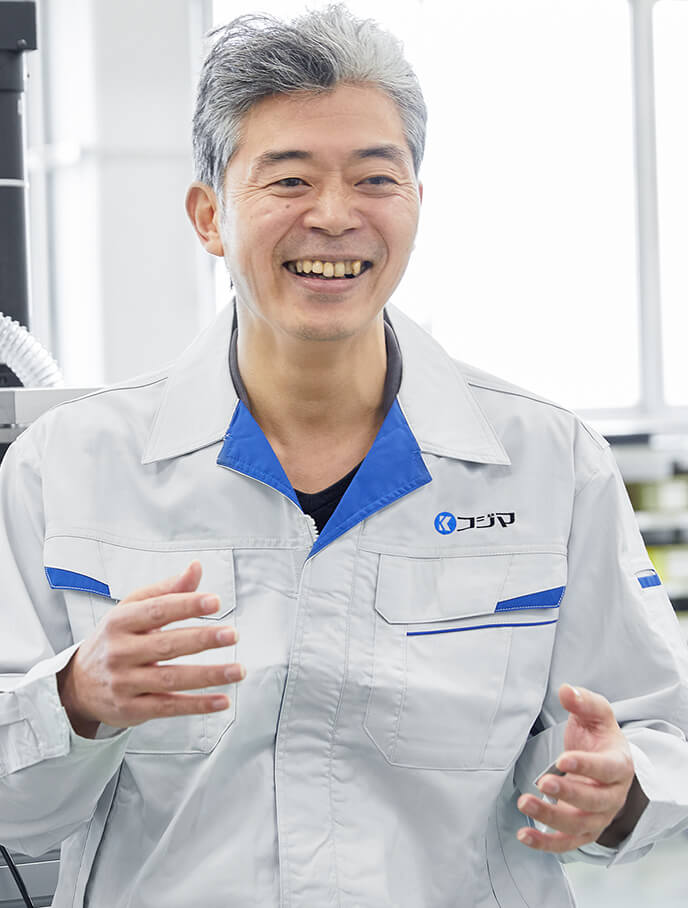
未来に向けて目下取り組んでいるのは「一貫業務化」です。部下には自分の担当を超えて何でもやってみなさいと指導しています。
例えば組付ならカシメも溶接も自分でやる。すると工程全体が理解でき、お客様のところに伺ってご提案ができるようになります。技術者がお客様と話すのも一貫業務のうちで、分野を超えて色々な知識を得ることによって、初めて知恵が出せるようになります。知識を増やすには自分で勉強するしかありません。
コジマにはいい制度が一つあって、毎月「技術連絡会」が開かれ、若手技術者が、自分が得た知見を経営トップの前で発表するのです。若手にとっては自分をアピールするチャンスであり、会社にとっては未来につながる技術を共有できるメリットがある。何より「やってみよう精神」が育つ機会になっていますね。
現在、客先にコジマ社員が出向して製品設計を学んでいますが、将来的にはお客様から業務委託をいただくのが目標です。そのために何でも作れる人を育てるのが私の仕事だと思っています。
コジマの社訓は「チェンジ」ですから、自動車関連に限らずニーズがあればどんな分野にも進むでしょう。そこがコジマの面白いところです。次は何に挑戦しようか、考えるとワクワクしますね。
部品・樹脂事業部 技術部 部長林 千泰
これまでコジマが手掛けたプロジェクトの一例をご紹介します。
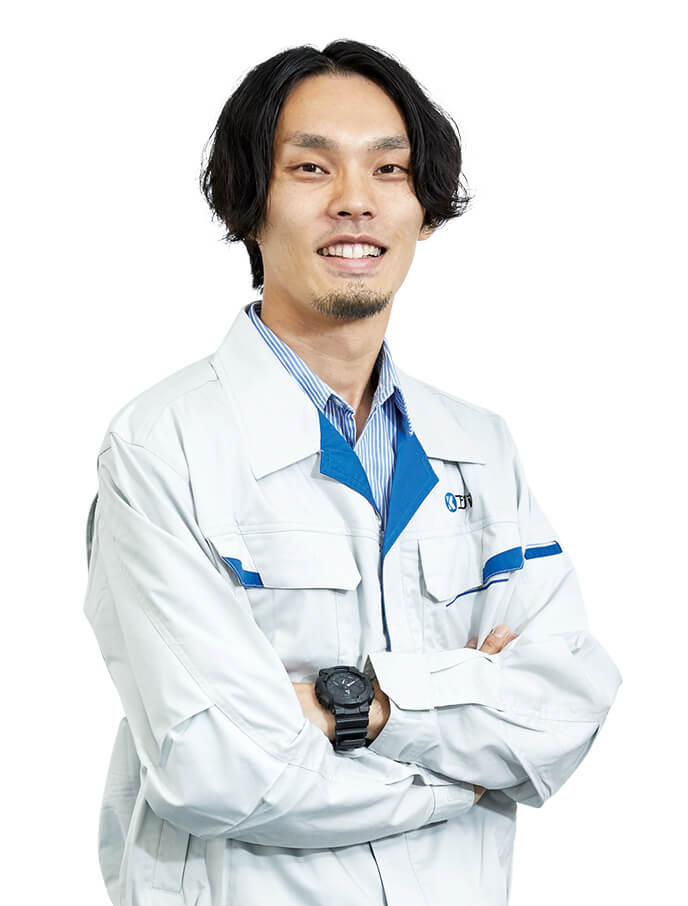
MOC(モーターオンキャリパー)
工程設計から関わり、効率的なモノづくりを実現!
これからのブレーキシステムの主流となる
「電動パーキングブレーキ」、
その量産化を目指して。
部品・樹脂事業部 営業部営業1課 主任プロジェクトメンバー早川 千尋(2012年入社)
新たなパーキングブレーキを作り出し、多くの自動車へ搭載するためのプロジェクト。
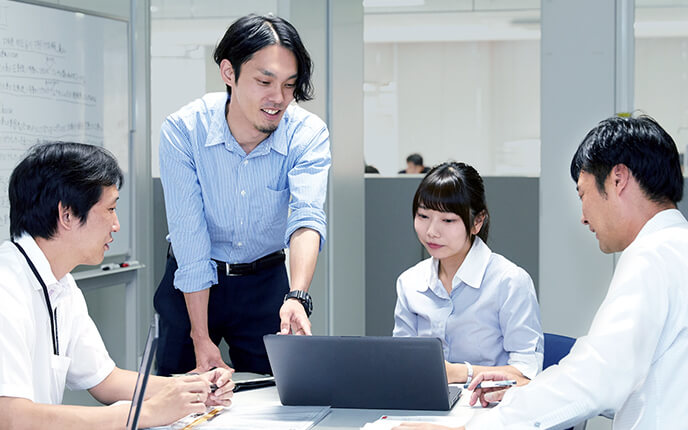
簡単なスイッチ操作やオート(自動)によってサイドブレーキの作動・解除を可能にした「電動パーキングブレーキ」。
これまでは、車輪部にパッドを押し付けて制動力を発生させるキャリパーとブレーキ機能を配線で繋ぐEPB(エレクトリックパーキングブレーキ)が主でしたが、今回は新たに、配線なしで制御するMOC(モーターオンキャリパー)の構想(部品点数低減によるコストダウン)が、自動車メーカーと弊社クライアントである部品メーカーの間で固まり、コジマが工程設計から生産、量産化まで携わることになりました。
専門知識ゼロの自分が、チームに支えられながら進んだ日々。
私がプロジェクトに参画したのは、物流の営業から異動してすぐのこと。
営業担当者として、クライアントと社内の各部署を繋ぐ重要なポジションにも関わらず、当時の私は図面が読めず、製品に対する専門知識も皆無でした。そのため、技術担当や品質担当にも打ち合わせに同行してもらい、社内では「こういう風に金型はできているんだよ」と教わる日々。部署の枠を越え、それぞれの専門知識を集結させることで、チームとして問題解決に挑むことができたのは、立場の上下や部署の枠にとらわれないコジマの社風があったからだと思います。
生産体制を整備し効率性を向上。その結果、増産依頼も続々!
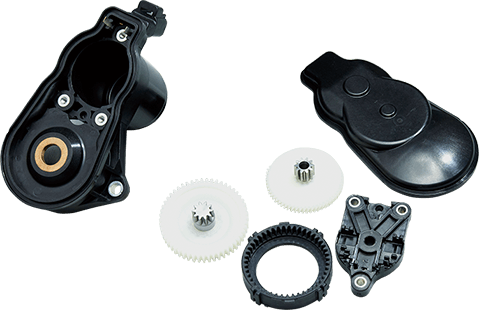
モノづくりでは、製品の不良率を下げることも重要な課題です。参画した段階で出来上がっていた図面では、その課題をクリアしづらい面がありました。そのため品質・コスト・生産性などを考慮しながら、より効率的にするための提案を行い、生産体制を整えました。
現在は、生産計画よりも1〜2ヶ月前倒しで次々と増産依頼がきている状態で、生産管理課などと調整を図りながら対応を進めています。
MOCは、今後のパーキングブレーキシステムの主流になるであろう製品です。自動車業界全体において、大きな期待を背負っていると思います。コジマがチーム一丸となって、その製品づくりに携わり、多くの自動車へ搭載される第一歩に関われたことは、私にとって大きな喜びであり、今後の仕事においての糧となっています。